Ultrasonic Thickness Gauge Calibration Procedure
Welcome to Cygnus Instruments, the leading provider of ultrasonic thickness gauges and calibration services. With years of experience in the industry, we take pride in supplying top-quality products and delivering exceptional services to our valued customers. As the original pioneers in ultrasonic thickness gauges, we have perfected our techniques to meet the evolving needs of various industries.
At Cygnus Instruments, we understand the importance of accurate measurements in your operations. That’s why we offer a comprehensive ultrasonic thickness gauge calibration procedure to ensure the reliability and precision of your equipment. Our fully qualified engineers are equipped with the latest tools and expertise to calibrate your instruments with utmost care and precision.
Whether you require calibration services or assistance with product selection, our dedicated team is always ready to assist you. We value customer satisfaction above all else and strive to exceed your expectations at every step.
Rest assured, Cygnus Instruments is highly accredited by numerous industry bodies, affirming our commitment to quality and excellence. We have earned the trust of professionals worldwide through our consistent delivery of reliable products and services.
To experience the Cygnus Instruments difference, contact us today at 01305 265 533. Our friendly experts are happy to assist you and ensure that your ultrasonic thickness gauges are operating at peak performance.
Importance of Proper Calibration for Ultrasonic Thickness Gauges
Proper calibration is crucial for ultrasonic thickness gauges to ensure accurate and reliable measurements. At Cygnus Instruments, we recognise the importance of maintaining precise thickness readings across various industries. Our ultrasonic thickness gauge calibration procedure guarantees optimal gauge performance, instilling confidence in your measurements.
Regular calibration is essential to uphold the integrity of thickness readings. By comparing gauge measurements against known calibration standards, we verify accuracy and adherence to required specifications.
Our experienced engineers meticulously calibrate your ultrasonic thickness gauge, following stringent procedures. Each calibrated gauge receives a certificate, serving as documented evidence of compliance with industry standards.
Accurate thickness measurements are critical for applications such as tube inspection, coating thickness analysis, and assessing component integrity. Precise measurements help identify structural weaknesses, ensure material thickness, and facilitate effective maintenance planning.
What Is Ultrasonic Thickness Gauge Calibration?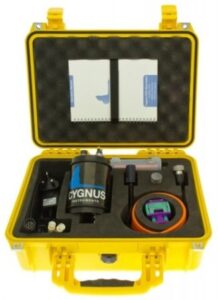
Ultrasonic thickness gauge calibration is a vital process that ensures the accuracy and reliability of thickness measurements. At Cygnus Instruments, we offer a comprehensive ultrasonic thickness gauge calibration procedure to maintain the precision of these instruments.
Calibration involves comparing the measurements of an ultrasonic thickness gauge against known calibration standards. By calibrating the gauge, we determine its accuracy and validate its adherence to required specifications. This process is essential for maintaining the gauge’s performance and ensuring that it provides accurate thickness readings.
During the calibration procedure, our experienced technicians follow meticulous calibration procedures. They calibrate the ultrasonic thickness gauge using advanced techniques and equipment to achieve precise results. Once calibrated, the gauge receives a calibration certificate, serving as documented proof of compliance with industry standards.
Accurate thickness measurements are crucial in various applications, including inspection systems, tube inspections, and coating thickness analysis. Calibrating the ultrasonic thickness gauge guarantees that the measurements are reliable, enabling effective decision-making and maintenance planning.
Equipment and Tools Required for Ultrasonic Thickness Gauge Calibration
To perform ultrasonic thickness gauge calibration, certain equipment and tools are necessary. At Cygnus Instruments, we ensure that our calibration process utilises the required resources to achieve accurate and reliable results.
The primary equipment used in ultrasonic thickness gauge calibration includes a precision thickness standard and a reference block. These standards are calibrated and traceable to recognised national or international standards, ensuring the accuracy of the calibration process. Additionally, specialised calibration software and a computer are employed to analyse and record the calibration data.
In addition to the standards, calibration procedures require the use of couplant, which is a gel or liquid medium that facilitates the transmission of ultrasonic waves between the gauge and the calibration surface. This ensures consistent and reliable measurements during the calibration process.
Our experienced technicians, equipped with the necessary tools, follow established calibration procedures to calibrate ultrasonic thickness gauges accurately. Once calibrated, the gauges are issued calibration certificates as proof of compliance with industry standards.
At Cygnus Instruments, we prioritise precision and adherence to calibration standards. Our state-of-the-art calibration laboratory and advanced inspection scanners enable us to deliver the highest level of accuracy and reliability in ultrasonic thickness gauge calibration.
Preparing for Calibration: Precautions and Safety Measures
When preparing for ultrasonic thickness gauge calibration, it is essential to take precautions and implement safety measures to ensure a smooth and secure process. At Cygnus Instruments, we prioritise safety to safeguard both the equipment and the individuals involved in the calibration procedure.
Before starting calibration, it is crucial to inspect the ultrasonic thickness gauge for any signs of damage or wear. Ensure that all cables, connectors, and transducers are in good condition and properly connected. Verify that the gauge is free from debris and contaminants that may affect the calibration results.
During calibration, it is important to follow established safety guidelines and wear appropriate personal protective equipment (PPE). This may include safety goggles, gloves, and protective clothing. Adhere to electrical safety measures, such as disconnecting the gauge from power sources before calibration.
To prevent accidents or damage, exercise caution when handling the calibration standards, reference blocks, and couplant. Follow proper handling procedures and secure the equipment in a stable position during calibration.
By adhering to these precautions and safety measures, you ensure a safe and successful ultrasonic thickness gauge calibration. Trust Cygnus Instruments for your calibration needs and experience a reliable and secure calibration process for your ultrasonic thickness gauges.
Step-by-Step Calibration Procedure for Ultrasonic Thickness Gauges
The calibration procedure for ultrasonic thickness gauges involves a systematic step-by-step process to ensure accurate and reliable measurements. At Cygnus Instruments, we follow a comprehensive calibration procedure for ultrasonic thickness gauges to maintain their precision and performance.
- Begin by inspecting the gauge for any physical damage or wear, ensuring that all cables and connectors are securely attached.
- Clean the transducer and gauge surfaces, removing any debris or contaminants that may affect the calibration results.
- Connect the gauge to the calibration block or known thickness standard, ensuring a stable and secure connection.
- Apply a suitable couplant to facilitate the transmission of ultrasonic waves between the gauge and the calibration surface.
- Initiate the calibration process by taking multiple readings at various thickness points on the calibration block.
- Compare the gauge readings with the known values of the calibration block, adjusting the gauge if necessary.
- Repeat the calibration process at different thickness points to ensure accuracy across the measurement range.
- Once the calibration is complete and the gauge readings align with the known values, issue a calibration certificate as proof of compliance with industry standards.
By following this step-by-step calibration procedure, we ensure that ultrasonic thickness gauges are accurately calibrated, providing reliable thickness measurements.
Verification and Adjustment of Calibration Standards
The verification and adjustment of calibration standards is a critical step in the ultrasonic thickness gauge calibration procedure. At Cygnus Instruments, we emphasise the importance of ensuring the accuracy and reliability of these standards to maintain the precision of the calibration process.
Calibration standards, such as known thickness blocks or precision thickness standards, are meticulously verified for accuracy. This involves comparing the measurements of the calibration standards against recognised national or international standards to ensure traceability.
If any deviations or discrepancies are identified during the verification process, adjustments are made to the calibration standards. These adjustments aim to align the standards with the known values, ensuring their accuracy and reliability for calibration purposes.
By verifying and adjusting calibration standards, we establish a solid foundation for the calibration process. This ensures that the ultrasonic thickness gauges being calibrated receive accurate reference measurements, enabling precise and reliable thickness readings in various applications.
At Cygnus Instruments, we prioritise the use of calibrated and verified calibration standards to deliver exceptional calibration services. Trust our expertise and commitment to accuracy when it comes to ultrasonic thickness gauge calibration.
Troubleshooting Common Issues in Ultrasonic Thickness Gauge Calibration
During the ultrasonic thickness gauge calibration procedure, certain issues may arise that require troubleshooting to ensure accurate and reliable results. At Cygnus Instruments, we have encountered and resolved common problems that can occur during gauge calibration.
One common issue is inconsistent or fluctuating readings. This can be caused by improper coupling between the transducer and the calibration surface. Ensuring proper contact and applying an adequate amount of couplant can help resolve this issue.
Another issue is inaccurate readings or deviations from known calibration standards. This can be caused by factors such as transducer misalignment, incorrect calibration settings, or electronic interference. Verifying the transducer alignment, reviewing calibration settings, and minimising external interference can help rectify this problem.
In some cases, the ultrasonic thickness gauge may exhibit a lack of sensitivity or difficulty in detecting thickness changes. This can be due to a worn or damaged transducer. Replacing or repairing the transducer can address this issue and restore sensitivity.
It is important to regularly calibrate and maintain ultrasonic thickness gauges to avoid these common issues. Trust the expertise of Cygnus Instruments to troubleshoot and resolve any problems that may arise during the calibration process. We are committed to delivering accurate and reliable calibration services for your ultrasonic thickness gauges.
How Do I Know If My Ultrasonic Thickness Gauge Is Due for Calibration?
Determining when your ultrasonic thickness gauge is due for calibration is crucial to maintain accurate and reliable measurements. Several indicators can help you determine if your gauge requires calibration.
First, consider the manufacturer’s recommendations for calibration intervals. Manufacturers typically provide guidelines on the recommended calibration frequency based on usage, environmental conditions, and industry standards. Adhering to these recommendations ensures the continued accuracy of your gauge.
Additionally, if you notice any inconsistencies or deviations in the thickness readings compared to known calibration standards, it may be an indication that your gauge requires calibration. Sudden changes in readings or a loss of precision can be signs that calibration is needed.
Another factor to consider is the industry regulations and standards. Many industries have specific calibration requirements that must be met to ensure compliance. If your gauge is used in a regulated environment, it is important to follow the specified calibration intervals to meet these requirements.
Lastly, if your gauge has been subjected to any physical damage or undergone repairs or modifications, it is advisable to have it calibrated to ensure its accuracy and reliability.
By paying attention to these indicators and following the recommended calibration intervals, you can ensure that your ultrasonic thickness gauge is calibrated and providing accurate thickness measurements.
What Are the Standards for Ultrasonic Thickness Gauge?
Standards play a crucial role in ensuring the accuracy and reliability of ultrasonic thickness gauges. These standards define the requirements and specifications that gauges must meet to deliver precise thickness measurements. At Cygnus Instruments, we adhere to industry standards to provide accurate and reliable calibration services.
One of the primary standards for ultrasonic thickness gauges is the calibration procedure itself. This procedure outlines the steps and guidelines for calibrating the gauges to establish their accuracy and reliability. It ensures that the gauge measurements align with known calibration standards.
Additionally, there are standards related to calibration verification. These standards provide methods and criteria for verifying the accuracy of the calibration process. Verification ensures that the calibration results are consistent and within acceptable limits.
Furthermore, there are standards related to the inspection and quality control of ultrasonic thickness gauges. These standards define the requirements for gauge performance, design, and functionality. They ensure that the gauges meet the necessary criteria for accurate and reliable thickness measurements.
What Is the Maximum Range of Ultrasonic Thickness Gauge?
The maximum range of an ultrasonic thickness gauge refers to the maximum thickness it can accurately measure. The range of ultrasonic thickness gauges can vary depending on the specific model and manufacturer.
At Cygnus Instruments, we offer a wide range of ultrasonic thickness gauges with varying maximum measurement capabilities. These gauges are designed to cater to different industry needs and applications.
The maximum range of ultrasonic thickness gauges typically spans from a few micrometres to several centimetres. The gauge’s transducer and associated software play a crucial role in determining the range and accuracy of thickness measurements.
It is important to select a gauge with an appropriate maximum range based on the specific requirements of your application. Whether you need to measure thin coatings or thicker materials, there is an ultrasonic thickness gauge available to suit your needs.
During the calibration procedure, the gauge is calibrated and verified within its specified measurement range to ensure accurate and reliable thickness readings.
What Is the Tolerance of Ultrasonic Thickness Gauge?
The tolerance of an ultrasonic thickness gauge refers to the allowable deviation or margin of error in its thickness measurements. Tolerance is an important factor in determining the accuracy and reliability of the gauge’s readings.
The tolerance of an ultrasonic thickness gauge can vary depending on various factors, including the gauge model, manufacturer specifications, and calibration procedures. It is important to consult the manufacturer’s documentation or guidelines for the specific tolerance values applicable to your gauge.
During the calibration procedure, the gauge is calibrated to ensure its measurements fall within the specified tolerance range. This calibration process involves comparing the gauge readings with known calibration standards of known thickness values.
The calibration procedure ensures that the gauge provides accurate and reliable thickness measurements within the defined tolerance limits. Calibration also helps identify and correct any systematic errors or deviations in the gauge’s measurements.
It is crucial to have the ultrasonic thickness gauge calibrated at regular intervals to maintain its accuracy and ensure compliance with industry standards. By adhering to calibration procedures and tolerances, you can trust that your gauge will provide precise and consistent thickness measurements for a wide range of applications.
Contact Us Today!
For precise and reliable ultrasonic thickness gauge calibration, trust Cygnus Instruments. Our experienced team is ready to assist you in maintaining the accuracy and performance of your gauges. Whether you require calibration services, information about the ultrasonic thickness gauge calibration procedure, or guidance on selecting the right gauge for your needs, we are here to help.
Contact us today on 01305 265 533 to speak with one of our knowledgeable professionals who can answer your questions and provide tailored solutions. Alternatively, you can fill out our convenient contact form on our website, and we will get back to you promptly. Our dedicated team will ensure your queries are addressed efficiently and professionally.
Reach out to us via email at sales@cygnus-instruments.com for any sales-related inquiries or further assistance. We pride ourselves on delivering exceptional customer service and reliable calibration services for ultrasonic thickness gauges. Trust Cygnus Instruments for all your calibration needs and benefit from our expertise and commitment to quality.